As the world continues its search for cleaner and more sustainable energy sources, hydrogen produced using renewable electricity is rapidly emerging as the most promising option for cross-sectoral decarbonisation.
With an energy content of 120 megajoules per kilogram (MJ/kg), hydrogen is nearly three times higher by weight and four times lower by volume compared to petrol (45.8MJ/kg) and diesel (45.5MJ/kg). Countries across the globe have recognized hydrogen’s potential to decarbonise multi-faceted sectors, including heat-intensive industries, medium-to-heavy mobility, and power. Countries like Germany, Australia, Japan, and Saudi Arabia have set ambitious strategies and roadmaps, with a clear intent of cross-sectoral decarbonisation.
With an atomic weight of 1, hydrogen is the lightest element and the most abundant element in the universe. It is non-toxic, colourless, and odourless. Despite its abundance, hydrogen does not occur naturally as a gas. Instead, it exists as a compound that can be extracted using various chemical processes.
The world produces around 70 million metric tonnes of hydrogen every year. Most of this is consumed for industrial applications, particularly for fertiliser production and petroleum refining. Almost all this hydrogen produced is through steam methane reforming (SMR) of natural gas.
Colour codes are assigned to hydrogen based on the feedstock/raw material used for production. For example, hydrogen produced through SMR is grey, SMR with carbon capture utilization and storage (CCUS) is blue, while green hydrogen is produced through water electrolysis. In addition, there are various other colour codes associated with the feedstock and production pathway, as seen in figure.
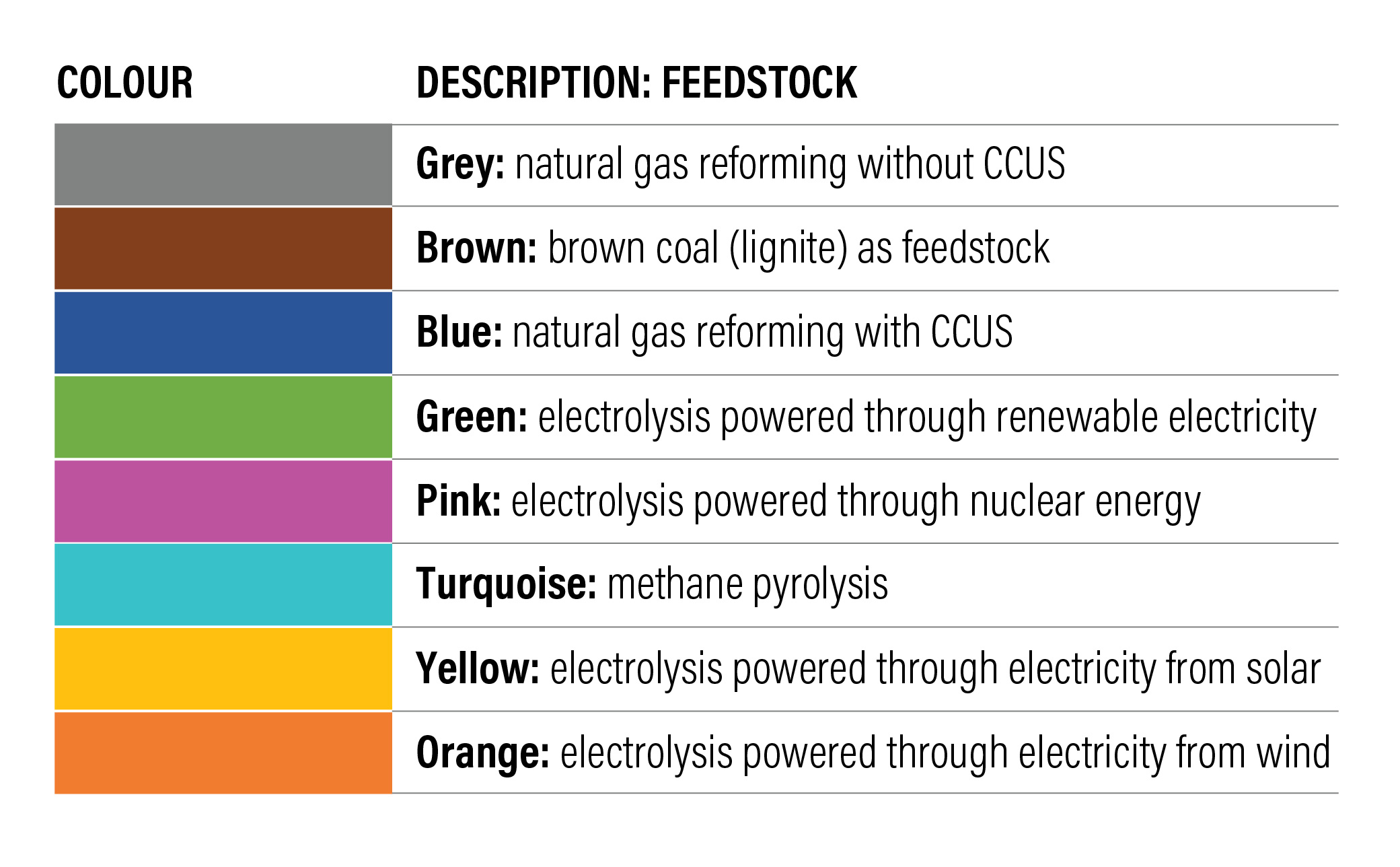
Some of the key hydrogen production pathways are SMR, electrolysis, gasification of organic matter, photolysis, and biological pathways using microorganisms.
Steam methane reformation of the natural gas involves the reaction of methane with steam at very high temperatures (700 – 1,000 degrees Celsius). in the presence of a catalyst. In this process, every kilogram of hydrogen produced generates around 10 kilograms of carbon dioxide (CO2). This established technology is carbon-intensive, accounting for 830 million tonnes of CO2 emissions annually. This is equivalent to the combined emissions of the United Kingdom and Indonesia. Current global hydrogen production can be decarbonised (blue hydrogen) by capturing CO2, storing, and utilizing it in non-emitting ways (CCUS) and by production of green hydrogen.
Hydrogen produced using electricity from renewable sources like solar and wind is termed green hydrogen. In this pathway, the water molecules are split into hydrogen and oxygen through electrolysers using renewable electricity. Deionized water is the feedstock. Hydrogen and oxygen produced are about 99.9% pure and have a significant economic value. Based on the type of electrolyser used, these are further classified into alkaline, polymer electrolyte membrane (PEM) and solid oxide electrolysers. Alkaline electrolysis (AE), operating at a temperature of 80-100 degrees Celsius, is a well-established and widely commercial process. Electrolyser catalysts used for this process include aqueous solutions of potassium hydroxides or sodium hydroxides.
Using polysulfonated membranes for splitting water molecules, PEM electrolysers are close to commercialization. The development of solid oxide electrolysers is still in the works, but the efficiency with the oxide is higher than that of alkaline electrolysers and PEM. This results in lower electricity usage per kilogram of hydrogen produced. Usage of rare platinum group metals like platinum, iridium, rhodium on cathode and anode makes the PEM electrolyser units expensive.
Alkaline (AE) and solid oxide electrolysers (SOE) are suitable low-cost alternatives. PEM electrolysis, however, has the advantage of quickly reacting to the fluctuations typical of renewable power generation. PEM water electrolysis systems also provide several advantages over the other two electrolysis technologies, such as higher hydrogen production, compact design, and greater energy efficiency.
Apart from the conventional hydrogen production pathways, biomass gasification is also gaining traction—more so in countries with high availability of organic resources such as agricultural or municipal solid waste. Gasification of biomass involves the incomplete combustion of feedstock at high temperatures. This process produces combustible gases such as carbon monoxide (CO), hydrogen (H2) and traces of methane (CH4). This mixture is known as syngas and can be separated to produce hydrogen at scale. Biomass is available from various sources, such as animal wastes, municipal solid wastes, crop residues, woody crops, agricultural wastes, sawdust, aquatic plants, and many others. No colour code is yet assigned to define hydrogen from biomass.
Given an array of ways hydrogen could be produced, it has a wide range of applications and can serve several end-use cases. It can facilitate cross-sectoral decarbonisation in industrial applications of hard-to-abate sectors like steel, cement, fertilizers, petroleum refining and chemicals, with a strong potential to decarbonise heavy mobility, power generation and function as an energy storage medium.
Source: wri-india.org