The recent approval of the production-linked incentive (PLI) scheme for domestic battery manufacturing signals India’s resolute intent to take up a deserved leadership role in the global energy transition while ensuring its energy future.
Approval of the scheme is timely, and the implementation cannot be delayed, as it would minimise any early mover advantage. Already between 2018, when the programme was first conceived, and 2020, global manufacturing capacity has increased threefold and is projected to increase by 400 percent in the next four to five years. China alone will account for almost 70 percent of this capacity. How aggressively manufacturers respond to the government’s scheme over the next two years will be critical for deciding India’s share in this global sunrise industry.
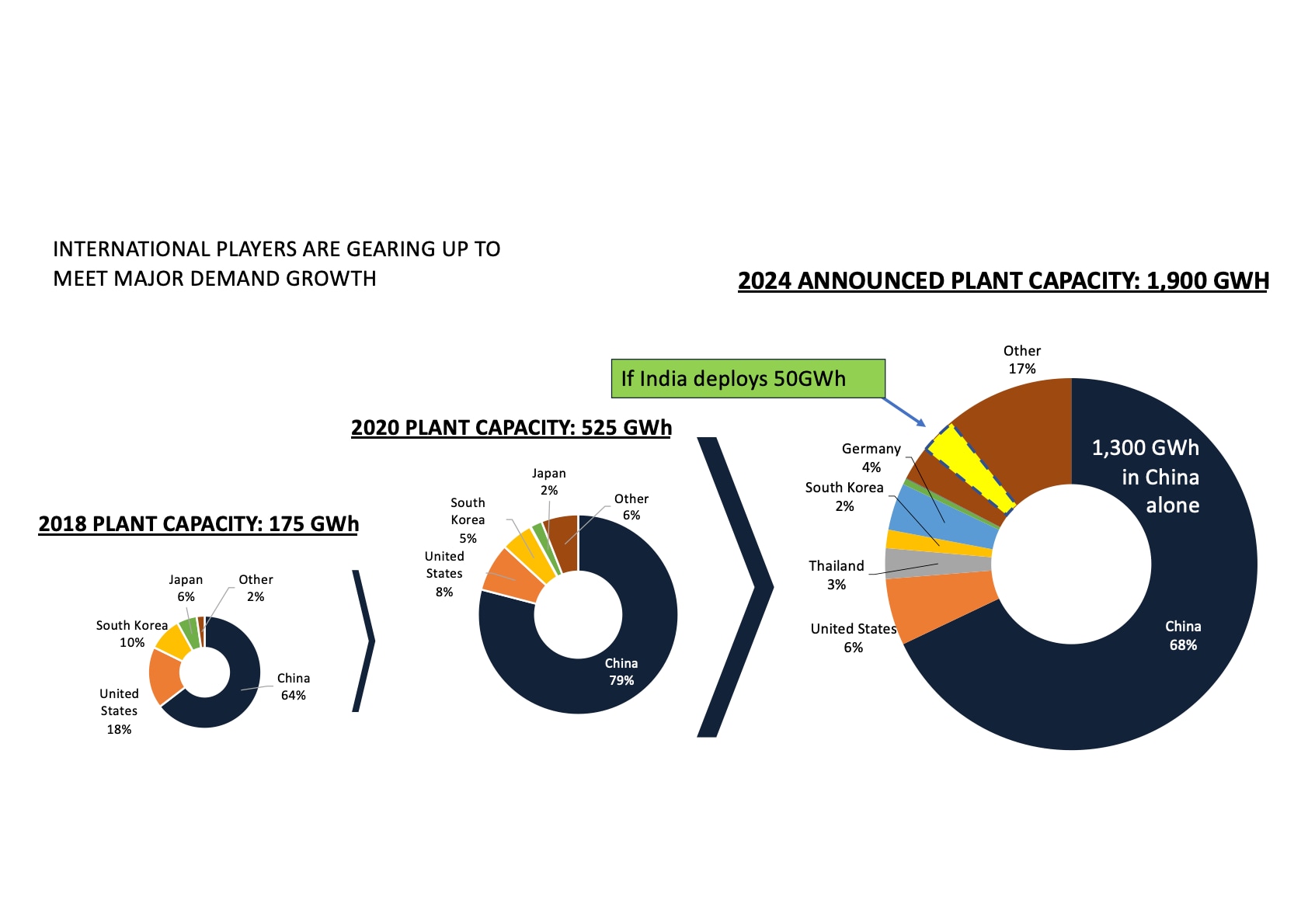
Figure: Emerging battery manufacturing ecosystem (Source: Bloomberg New Energy Finance, Long-term Energy Storage Market Outlook 2040; BNEF Energy Storage Data Portal, accessed in Dec 2020)
The heated race for dominance in battery manufacturing highlights the critical need for India to secure the material supply chain of key minerals and metals such as graphite, lithium, nickel, cobalt, manganese, etc. (for the current set of battery technologies). India lacks many of these critical metals, most importantly nickel, cobalt and lithium.
Many of these resources are highly concentrated geographically. Cobalt, for example, is predominantly mined in the Democratic Republic of Congo (DRC), a country mired with political risks. Many manufacturers are exploring low and no-cobalt battery architectures. While India should plan to secure the material supplies for currently predominant battery technologies, in the long-term, Indian manufacturers should focus on developing alternative chemistries using less resource-constrained materials.
The PLI scheme is designed to encourage such a movement towards better performing next-generation technologies that improve material efficiency. India should also continue encouraging Research and Development (R&D) towards newer chemistries and technologies. But given the inevitable dependence on international trade in near-to-medium term, the challenge is to manage the risk over the next five to seven years and ensure that the monopolistic control over metals and their value chain doesn’t happen.
The obvious strategy, and a lesson from the oil and gas industry, is to do with asset and equity ownership in the mines of producing countries. These could be both a government as well as private sector endeavour. In this regard, India has already signed one memorandum of understanding (MoU) with Bolivia. India should become part of the metal refining and processing value chain.Many of the countries, where resources may be located, may not actually have the right industrial base to process ores for commercial purity. While China currently dominates it, given the expected growth, there is still a large room for new emerging players. Further, as the International Energy Agency (IEA) recommends in its latest report on The Role of Critical Minerals in Clean Energy Transitions, supply chain resilience must be developed through regular market assessments and by ensuring strategic stockpiling where appropriate.
Another critical strategy would be recycling.
Recycling will need to form a big part of metal recovery, especially for countries such as India. India is very cognizant of the need for recycling. Government interest and institutional knowledge are clearly there and private entities are embarking on becoming part of the recycling industry. Given the lack of certain metals, India also sees this more from a supply security place.
There is this concept of urban-mining as opposed to recycling, whereby recycling is seen as an alternate resource for metals and minerals. Drafting regulations and standards pertaining to battery recycling will be necessary to cement the growth of this sector.
Recycling, however, would not close the loop completely. It can only recover a limited portion of metals and minerals and at a cost. Mining will still be required. Given the industry-specific nature of the risk, companies indulging in manufacturing should explore vertical integration and strategic partnerships with mining (and recycling) companies to reduce the risk to their own supply chain.
Where increased mining is unavoidable, it should be climate-smart. According to the World Bank, this includes, out of many things, making mining less CO2 intensive and efficient, ensuring adequate environmental governance and regulatory framework, low-carbon supply chain management, making mining companies adopt a circular economy approach, de-risking investment in low-carbon mining, and leveraging carbon finance.
Given the size of its market, India can and must play its part in ensuring a transparent, rule-based global environment for international trade, mainstreaming higher environment and social standards and in spearheading the movement towards recycling and material efficiency through research and development as well as market building endeavours. Only then can India’s battery manufacturing ambition and its larger energy transition story be truly secure and sustainable.
Source: cnbctv18.com